Our Approach
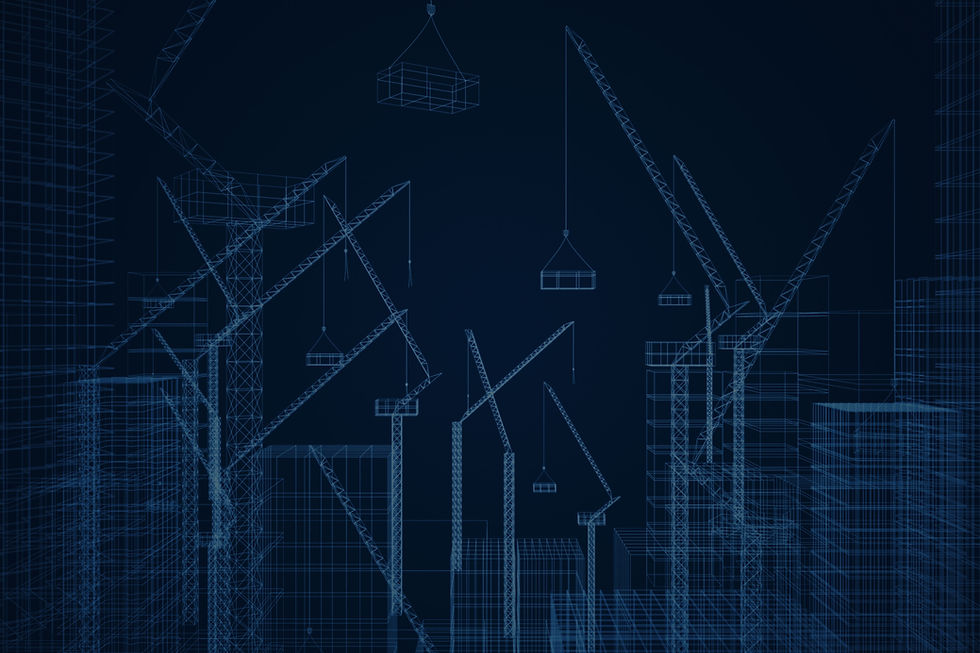
At MLP Solutions, our approach is rooted in collaboration, innovation, and a commitment to excellence in every project we undertake. We believe that successful construction begins long before the first brick is laid, which is why we prioritize understanding the unique goals and vision of each client. By fostering open communication from day one, we ensure that every phase of the project is aligned with our clients’ expectations and needs.
​
We start with a detailed pre-construction process, performing thorough feasibility studies, budgeting, and site assessments to identify opportunities for value engineering and efficiency. This allows us to mitigate potential risks and ensure projects stay on schedule and within budget. Our team works closely with clients to provide transparent, data-driven insights, helping to make informed decisions that drive the project forward seamlessly.
​
Innovation is at the heart of our operations. Whether utilizing the latest in sustainable building techniques or implementing cutting-edge construction technologies, we’re always looking for ways to push boundaries and improve outcomes. We view every project as a chance to engineer smarter, more sustainable solutions, while maintaining a high level of craftsmanship and attention to detail. By treating each building as a system, we ensure that all components work together harmoniously, delivering not just a finished structure but an optimized, high-performance environment. We are a circular solutions company - Precon, Engineering, Planning, Procurement, and Installation!
​
Ultimately, our approach is centered on integrity and ownership. We take pride in delivering on our promises and being accountable for every aspect of our work. From start to finish, MLP Solutions is committed to exceeding expectations, building lasting relationships, and ensuring that each project reflects the quality, innovation, and value our clients deserve.
Preconstruction
Communication
Effective communication during the preconstruction phase creates a strong foundation throughout the project lifecycle.
Planning and Design
MLP Solutions collaborates with design and engineering teams, lending our expertise to ensure the constructability of your project.
Budgeting and Cost Estimating
Our cost analysis and supply chain intelligence enable us to create detailed, comprehensive budgets and cost estimates that account for value engineering opportunities, material and labor costs, and economic risk factors.
Risk Management & Mitigation
We allocate effort to identify, manage and mitigate risk. This includes identifying potential hazard, assessing the potential impact of those hazards, and developing strategies to mitigate or eliminate those risks.
Procurement
Our procurement professionals negotiate contracts that ensure the necessary materials and equipment are on-site when needed, giving you the assurance that your project will be completed on time.
Construction
Management
Design-Build
With the goal of streamlining the project process and reducing costs, this approach offers more efficient and cost effective process and better alignment of goals between the design and construction teams
Construction Management -
At Risk
The construction management team is responsible for both the design and construction of the project and assumes the risk for any cost-overruns or schedule delays. The benefits of this approach include a more cohesive team and a higher level of accountability
Integrated Project Delivery
Our cost analysis and supply chain intelligence enable us to create detailed, comprehensive budgets and cost estimates that account for value engineering opportunities, material and labor costs, and economic risk factors.
Target Value Design
A method of designing and constructing projects that focuses on achieving a specific cost target while still meeting the functional and aesthetic requirements ofthe project. This approach involves collaboration between the design team, the owner, and the contractor to identify cost-saving measures and optimize the design to meet the target budget.
Project
Management
Initiating
Define the project and gain authorization to begin. Develop the Project Charter. Identify stakeholders and create the Stakeholder Register. Define high-level goals, constraints, assumptions, and deliverables.
Secure initial approvals and funding.
Planning
Establish the roadmap for how the project will be executed, monitored, and closed. Develop the Project Management Plan.
Define project scope, objectives, and deliverables (Scope Management Plan).
Create a Work Breakdown Structure (WBS).
Plan Schedule, Cost, Risk, Quality, and Communication.
Identify required resources and responsibilities (Resource Management Plan).
Prepare for risk response with a Risk Management Plan.
Executing
Perform the work defined in the project plan to achieve project goals. Direct and manage project work. Acquire, develop, and manage the project team.
Implement risk responses and quality management. Conduct procurements for external resources or vendors. Communicate updates and engage stakeholders.
Monitoring and Controlling
Track, review, and regulate project performance to ensure it stays on track. Monitor project work against the baseline (scope, schedule, and cost).
Perform integrated change control to manage project changes. Validate deliverables and control quality. Identify and manage project risks continuously. Communicate project performance to stakeholders.
Closing
Finalize all activities and formally close the project.
Obtain formal acceptance of deliverables from stakeholders.
Close procurements and contracts. Document lessons learned for future projects.
Archive project documentation and release resources.
Celebrate the project’s success with the team and stakeholders.

Lean
Construction
Value Generation
Deliver what the client truly values. Align all project activities with customer needs to ensure resources are spent on adding meaningful value rather than unnecessary tasks.
Flow Efficiency
Ensure a smooth, uninterrupted flow of work by balancing workloads, removing bottlenecks, and aligning resources with demand.
Waste Reduction
Identify and reduce waste in all forms, such as:
Overproduction (e.g., ordering excess materials).
Waiting (e.g., delays between project stages).
Defects (e.g., rework due to poor quality).
Inefficient transportation or motion.
Continuous Improvement
Constantly seek better ways to execute tasks, solve problems, and deliver results. Use techniques like root cause analysis and regular feedback to refine processes.
Respect for People
Value and empower everyone involved, from workers to stakeholders. Encourage collaboration, open communication, and mutual trust to improve morale and performance.